當GE的增材制造負責人Mohammad Ehteshami談到3D打印時,他用“頓悟”來形容3D打印帶來的沖擊感。他意識到增材制造將顛覆公司當前的設計和制造方式,這既讓人感到興奮,但也感到不安。3D打印開啟了航空航天制造領域的全新潛力,但是這項技術也可以消除GE積累了多年的傳統加工領域的寶貴經驗,新的起跑線上,這項技術將給GE的財務模式帶來很大的壓力。
不僅僅是GE這樣的大型公司需要對改變做出充分的準備。面向2018年,Gartner預測3D打印將在眾多應用領域改變當前的商業模式。研究突出顯示了三個行業:醫療設備、航空航天、消費品。
預測:到2021年,75%的新型商用和軍用飛機將搭載3D打印引擎、機身和其他部件。
航空航天業是第一批采用3D打印的行業之一,雖然原型制造仍然是所有行業3D打印的主要應用范疇,但航空航天領域已經積極地將3D打印的應用推向模具、夾具和零件生產方面。例如經過20多年的經驗積累,波音公司在四個國家的20個地點進行了增材制造,在商業和國防項目中,有超過5萬個3D打印部件正在飛行。
GE航空新型先進渦輪螺旋槳發動機設計將855個常規制造零件減少至12個3D打印零件,并且功率增加10%,節省20%的燃料,縮短開發周期并降低設計成本。
不僅僅是GE這樣的大型公司需要對改變做出充分的準備。面向2018年,Gartner預測3D打印將在眾多應用領域改變當前的商業模式。研究突出顯示了三個行業:醫療設備、航空航天、消費品。
預測:到2021年,75%的新型商用和軍用飛機將搭載3D打印引擎、機身和其他部件。
航空航天業是第一批采用3D打印的行業之一,雖然原型制造仍然是所有行業3D打印的主要應用范疇,但航空航天領域已經積極地將3D打印的應用推向模具、夾具和零件生產方面。例如經過20多年的經驗積累,波音公司在四個國家的20個地點進行了增材制造,在商業和國防項目中,有超過5萬個3D打印部件正在飛行。
GE航空新型先進渦輪螺旋槳發動機設計將855個常規制造零件減少至12個3D打印零件,并且功率增加10%,節省20%的燃料,縮短開發周期并降低設計成本。
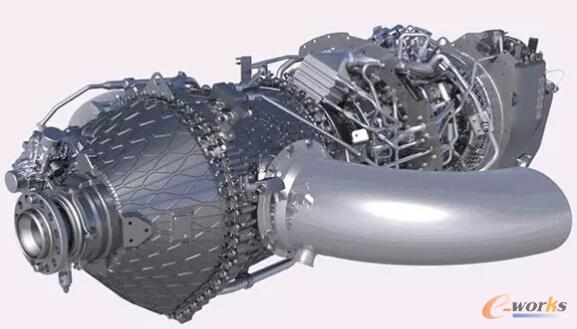
圖1 GE航空公司的先進渦輪螺旋槳發動機
預測:到2021年,25%的外科醫生將在手術前在患者的3D打印模型上進行練習。
醫院和專業實驗室提高了集成醫療成像、CAD建模和3D打印工作流程,醫院在不斷的提高3D打印硬件、軟件和服務的投資。Gartner估計近3%的大型醫院和醫學研究機構已經具備了在內部的3D打印實力。
在這方面,GE醫療在探索是否能將CT掃描數據快速直接完成建模過程,并直接傳送到3D打印機,從而切斷中間手工轉換的幾個階段。
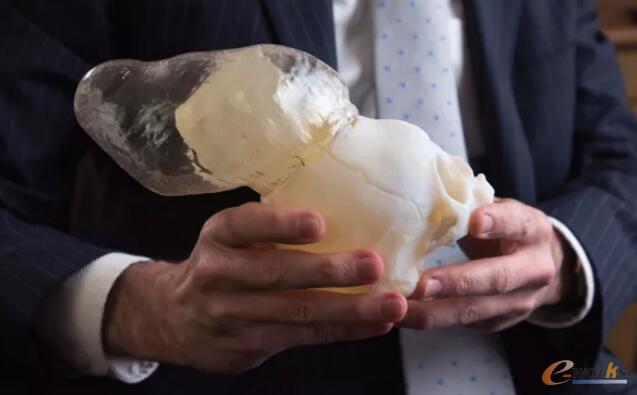
圖2 兒童外部大腦物質的3D打印外科模型
而不僅僅是醫療模型,3D影像VR技術也被應用到手術練習方面。這方面,3D Systems的虛擬現實手術室(VR OR)系統可以幫助患者轉移對生理病痛的注意力,放松心情,從而為患者減輕壓力和疼痛。也可以通過定制的VR設備進行后續的康復治療。另一方面,醫生可以通過虛擬現實頭顯實時遠程觀看資深醫生進行手術,獲取相關的經驗。
隨著3D打印技術的不斷完善和其他技術的不斷完善,3D打印技術將從教學醫院和專業中心擴展到更廣泛的醫院系統。波士頓兒童醫院就是一個例子,他們采取團隊方式進行培訓和手術計劃。臨床醫生、工業工程師、設計師、模擬專家、病人護理隊都參與其中。隨著更多的3D打印功能上線,Gartner希望外科醫生和醫務人員能夠以“交鑰匙”的方式提高3D打印對健康領域的應用。3D打印技術也將從隱秘的后臺實驗室轉移到最前沿,作為改善手術訓練和模擬戰略的一部分。
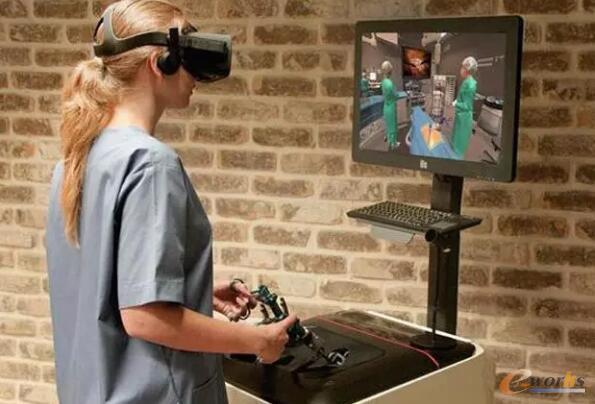
圖3 3D Systems的VR系統
預測:到2021年,20%的企業將建立內部創業公司來開發新的3D打印產品和服務。
企業現在正以閃電般的速度發展,技術進步更快。已發展成熟的公司還需要不斷面臨創業公司和新興公司的競爭。為了與這些快速發展的公司進行競爭,公司內部出現了鼓勵內部創業的情況,以快速跟蹤3D打印技術和其他創新技術可能會對當前業務產生的威脅。
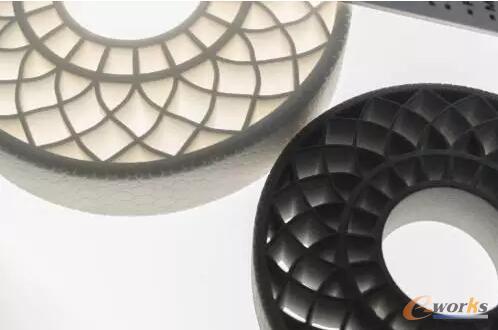
圖4 巴斯夫3D打印的熱塑性無氣輪胎概念
在過去的幾年里,空中客車、巴斯夫、通用電氣等一大批大型企業已經建立了工業規模的3D打印內部創業模式。這些公司能夠加速將3D打印集成到他們自己的制造流程中,以使用傳統的制造方法來制造難以實現或成本太高的部件。3D打印內部啟動的概念正在迅速獲得重視,并將在未來幾年變得非常普遍。一家內部創業的公司可以使母公司把他們最聰明的一些人的注意力集中在3D打印創新上,同時保護他們現有的收入來源不受干擾。
預測:到2021年,40%的制造企業將建立3D打印卓越中心(COE)。
制造領域的很多企業已經實施了3D打印技術。拿西門子來說,西門子通過英國林肯工廠及其收購的英國3D打印公司Materials Solutions,對SGT-400燃氣輪機的葉片進行了重新設計,3D打印技術的葉片具有完全改進的內部冷卻幾何制造。而葉片的批量生產通過位于美國Worcester的工廠來完成。在這里,西門子林肯工廠就扮演了卓越中心的角色。
2017年,GKN正式在牛津郡阿賓登開設了一個新的卓越中心。新中心將致力于為GKN的汽車業務開發先進制造技術,包括定制化的3D打印零部件、電動傳動系統、復合材料等。GKN將使用3D打印技術來重新設計和制造下一代車輛的定制零件。

圖5 GKN的汽車卓越中心
奧迪與德國工業級3D打印制造商EOS建立了伙伴關系,雙方的合作涉及到奧迪全面部署工業增材制造技術,并奧迪在英戈爾斯塔特建立相應的3D打印卓越中心。通過這種合作關系,奧迪從EOS獲得的支持包括:提供適合的增材制造系統和生產流程,共同進行3D打印的應用開發,構建內部的增材制造知識,將奧迪工程師培訓成為內部增材制造專家。
在過去幾年中,不僅僅是這些企業,大多數大型企業已經建立了工業規模的3D打印COE(Center of Excellence)卓越中心(例如波音、強生、勞斯萊斯、寶馬、GE等)。在這樣做的同時,他們已經將3D打印相關的工作流程整合到關鍵業務流程中。卓越中心的好處是能夠更好地完善現有的3D打印方法并為推廣3D打印技術做準備,同時創建度量標準,重點改進設計創新,健全關鍵流程標準化,并重點改進質量和檢驗流程。3D打印卓越中心還可以作為供應鏈合作伙伴的培訓機構或體驗中心,并未企業內部的團隊提供培訓機會。
目前,雖然中型企業制造商開始效仿卓越中心的理念,但投資較少。這些公司傾向于將3D打印服務外包出去,因為所需的資金成本和專業勞動力往往是一個太大的壁壘,使得這些中型企業無法自行承擔卓越中心的運轉成本。
但是3D打印卓越中心又是企業發展的加速器,長期目標方面卓越中心可以成為設計和制造過程的無縫銜接。如果成功,卓越中心在產品的設計、制造和維護中如何引入3D打印技術都具有廣泛的意義。
企業可以借助3D打印廠商的力量來進行卓越中心的部署。在這方面,可以參考一些現成的做法。例如,林德集團因EOS提供的支持在很短的時間內成功地積累了增材制造領域專業設計知識并測試了新的產品。通過與EOS的合作,林德集團的競爭地位得到了顯著的提升。
預測:到2021年,世界前100家消費品公司中有20%將使用3D打印來制造定制化的產品。
快速產品原型是消費品公司目前最廣泛使用3D打印技術的應用。Fishman(吉他放大器)和聯合利華(家用產品)等公司已經在通過3D打印技術來大幅縮短設計和生產時間,節省成本。不過快速原型并不是消費品行業唯一相關的應用領域。
3D打印也可能對消費品公司供應鏈產生重大影響。定制化生產可能減少庫存,這種面向本地消費的本地生產的轉變將使消費品公司能夠重新思考他們的商業模式。例如,名為Raceware的公司使用3D打印技術來創建自定義的自行車零件。
而阿迪達斯正在推進運動鞋的數字化及制造基地離散化趨勢。早在2015年8月的時候,阿迪達斯就喊出了“2016年在德國生產出第一雙私人訂制運動鞋樣品”的口號。從那時開始Speedfactory走入了人們的視野。在阿迪達斯位于東南亞的傳統制造工廠里,每年生產大約7.2億雙鞋,但這些生產過程緩慢而不具備靈活性。而在阿迪達斯位于德國的“Speedfactory”速度工廠里,則可以將從模型到生產的時間縮短到一天。
雖然,增材制造將不可能完全取代消費品市場的大量生產模式。但我們不可否認,產品的批量和產品的生命周期正在急速縮小和縮短。事實上,就拿鞋業來說,2011年匹克關閉2000家門店,因為以前一個貨柜能賺5萬元,而后來只剩幾千元的利潤。以前,同款式的鞋可以做20萬雙。而到2011年同款式的鞋也就兩三千雙,還要不同顏色的。
的確,消費者變得更加自我,更加挑剔了。這倒逼著消費品市場尋求更加靈活的生產方式。與傳統制造技術相比,現在的公司必須學習如何在何時何地使用3D打印技術,從而更有意義地進行批量與成本效益的權衡。