一、企業介紹
東莞勁勝精密組件股份有限公司成立于2003年,是東莞第一家創業板上市公司。公司于2015年成為智能制造首批試點企業,同時,公司“移動終端金屬加工智能制造新模式”項目是國家工業和信息化部全國首批智能制造專項項目。公司基于智能制造專項項目的建設經驗,將繼續完善集高端數控機床、國產機器人、自動化設備、國產系統軟件等于一體的智能制造產品和服務體系,打造智能工廠系統集成總承包服務和整體智能工廠改造解決方案的能力。除智能制造業務外,另還有其他業務包含:消費電子產品精密結構件業務、高端裝備制造業務。
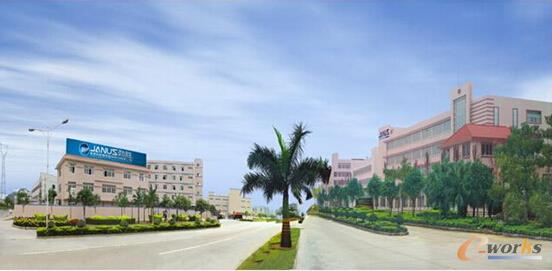

東莞勁勝精密組件股份有限公司
二、創新背景介紹
工藝創新
采用“三國”:國產智能設備、國產數控系統、國產工業軟件,打造了一個擁有200臺CNC鉆攻中心、81臺工業機器人,自感知、自決策、自執行的國內高端“移動金屬加工智能制造新模式”的智能化數字車間。
使生產制造過程實現:“裝備自動化”、“工藝數字化”“過程可視化”、“決策智能化”“信息集成化”“生產柔性化”。
創新背景
3C制造業基本情況及移動終端產品對智能制造系統的需求。由蘋果手機引領的金屬外殼化趨勢引發了3C 產業以 CNC為核心的智能制造系統與裝備需求的爆發式增長。然而,手機行業的產品升級和消費個性化需求的快速增長對高精密結構件產品的研發與制造行業提出了更高的要求。由于東莞勁勝精密組件股份有限公司(以下簡稱“勁勝精密”或“公司”)擁有三星、中興、華為、OPPO 等豐富多元的客戶資源,與其他廠相比而言生產的品類更多,這加劇了對其制造能力和制造效率的挑戰。同時,由于產品升級越來越快,對交期管控越來越嚴格,零部件制造環節對機器人靈活性和精確度的要求、對智能制造系統中計劃、物流及質量精準管控的要求都越來越高。
勁勝精密自成立以來,一直非常注重智能制造系統在設計、制造環節的應用。截至2015年4月,勁勝精密已通過自主開發和外部合作方式,先后建立了ERP、 PDM、MES等系統,打造出適合自身需求的數字化制造解決方案,為勁勝精密近年來主營業務飛速發展提供了強有力的保障。ERP系統管理規模和范圍涉及全面,實現了公司七個事業部31個車間的運營級別業務流程在統一平臺進行管理。其精益生產系統除保證車間生產過程管理外,還將生產設備如數控機床等做到了多種客戶端可視化展示。同時,勁勝精密也非常注重制造裝備的升級改造工作,僅在高速鉆攻加工環節方面就投入2500臺智能化數控 設備,并計劃3年內完成總共6000臺高速鉆攻中心設備的配置,主要用于移動終端中的智能金屬手機外殼及相關金屬部件的精密加工制造。
為了面向未來多品種、高品質、快速交付的市場要求,勁勝精密需要進一步的提升產品質量穩定性、提升產品加工效率、降低產品成本。因此就需要通過本項目盡快提升企業的智能制造水平,并通過項目的成果,帶動我國高精金屬加工行業的智能制造水平的總體提升。
實現高速高精國產鉆攻數控設備、數控系統 與機器人的協同工作,在業內率先實現裝夾環節采用機器人代替人工操作,節省70%以上的人力;建立基于物聯網技術的制造現場“智能感知”系統,改造升級 現有智能化系統,建立全制造過程可視化集成控制中心,實現對加工中心、機器人、物流裝備等的全面支持,最終實現少人化協同化生產。
三、企業具體實施的創新舉措
1)國內全行業首家大量采用國產數控系統配套核心關鍵裝備的智能化車間: 基于完全自主知識產權的國產數控系統,配套于移動終端產品核心部件智能制造車間關鍵裝備高速鉆攻中心裝備和工業機器人,不僅打破國外技術與市場壟斷,同時,其自主知識產權的總線通信技術保障了智能化車間裝備的數據安全和使用 信息安全;
2)建立基于物聯網技術的制造現場“智能感知”系統:將制造生產過程中 的關鍵重要部件、制造資源(如刀具、夾具、托盤、卡板等)結合物聯網技術進行“智能感知”,使其在在每個生產環節上能夠實時主動告知其位置、生產狀態、工藝參數等信息,并將數據傳遞至上層的決策系統,實現“物物相聯”的制造現場“智能決策”;
3)構建基于數據驅動的三維仿真模型:采用輕量化及分塊分層算法以保證工廠及設備大規模數據的快速顯示,采用基于時間軸的動畫插值技術實現離散位移數據的平滑運動顯示,規劃物流模型運動路徑,實時檢測三維模型之間的碰撞以檢驗模型運動的合理性,建立三維模型運動與數據變量的實時關聯,最終實現三維模型的數據驅動;
4)實現基于三維的工藝協同:實現工藝軟件、知識庫與三維 CAD(Computer Aided Design)的集成,實現基于 MBD(Model Based Definition)的制造特征定義與信息提取,打通了幾何特征模型和制造特征模型之間的聯系;將工藝知識融 入到后端的自動化設備(數控機床、焊接機器人、自動切割機)應用中,實現三維工藝從產品設計--工藝--智能制造的貫穿式應用,全面提升行業加工智能性 和效率;
5)建立全制造過程可視化集成控制中心:將計劃、執行、物流、質量等業務板塊的實時決策數據與圖表集中展示,打通各功能域的關聯關系,建設可視化集成控制中心,打造實施過程數據驅動的制造車間決策支持平臺,支持計劃、物流、質量、采供等多功能組織的全局協同生產與調度;
6)構建基于企業私有云的分布式協同制造服務體系:通過建立面向 3C 制造的企業級私有云制造服務平臺,將勁勝精密分布在不同地域的7個事業部35個車間通過企業私有云進行連接,打造支持企業內多工廠協同制造的云服務模式,提升企業異地協同制造能力;
四、該創新在業內產生的影響
國家層面:采用國產智能裝備、國產數控系統、國產工業軟件實施智能制造,對提升國產智能制造產品的核心競爭力具有示范意義,為實施“中國制造2025”探索途徑。
區域層面:在東莞制造業名城實施,并創新設計一系列政策,對于勞動力密集型的區域如何通過智能制造實現轉型升級具有示范意義。
行業層面:有3C行業的典型企業牽頭,對于促進3C產業智能制造升級意義重大,同時可推廣到其它行業。
企業層面:不僅幫助企業體質增效,同時滿足未來市場的個性化、定制化的產品需求,更促進企業向制造服務業“智能工廠系統解決方案服務商”的升級。
五、該創新的核心價值體現
具有領先市場優勢的 3C 行業 CNC 鉆銑中心:開發的 3C 行業 CNC 鉆銑中心集成了具有自適應能力的多種加工模式切換功能,實現不同結構和材料特性的產品零件對象的高速精密加工。同時,針對 3C 產品加工的智能伺服動 態制動技術,高速鉆攻中心行程范圍小且加工速度高,在機床遇故障需要快速 停機時,通過伺服動態制動技術的實現,實現移動軸的快速制動,相關技術與 產品性能、功能達到國際先進水平。
在全國智能制造示范項目廣泛應用的智能感知技術與器件:完成和設計開發了工業 RFID、機器視覺和智能感知系列化核心技術,設計并實現了配合機器人、自動化設備、機床、信息系統的核心裝置,實現了傳 感器的多方位結合,獲得國家技術發明二等獎1項,發明專利3項,實用新型專利2余項,參與起草了超高頻電子標簽國家標準,長期致力于電子制造裝備 研制開發工作,在 IC 裝備制造領域處于國內前列。
實現“三國”的智能制造集成應用示范:由勁勝精密牽頭、工研院和華中數控參與建設的全國智能制造示范點,實現了“國產裝備、國產數控系統和國產軟件”的自主知識產權產品應用。
1.國內全行業首家大量采用國產數控系統配套核心關鍵裝備的智能化車間:基于完全自主知識產權的國產數控系統,配套于移動終端產品核心部件智能制造車間關鍵裝備高速鉆攻中心裝備和工業機器人,不僅打破國外技術與市場壟斷,同時,其自主知識產權的總線通信技術保障了智能化車間裝備的數據安全和使用信息安全。
2.建立了基于物聯網技術的制造現場“智能感知”系統:將制造生產過程 中的關鍵重要部件、制造資源(如刀具、夾具、托盤、卡板等)結合物聯網技術進行“智能感知”,使其在在每個生產環節上能夠實時主動告知其位置、生產狀態、工藝參數等信息,并將數據傳遞至上層的決策系統,實現“物物相聯”的制造現場“智能決策”。
3.構建了基于數據驅動的三維仿真模型:采用輕量化及分塊分層算法以保證工廠及設備大規模數據的快速顯示,采用基于時間軸的動畫插值技術實現離散位移數據的平滑運動顯示,規劃物流模型運動路徑,實時檢測三維模型之間的碰撞以檢驗模型運動的合理性,建立三維模型運動與數據變量的實時關聯,最終實現三維模型的數據驅動。
4.實現了基于三維的工藝協同:實現工藝軟件、知識庫與三維 CAD 的集成,實現基于 MBD 的制造特征定義與信息提取,打通了幾何特征模型和制造特征模型之間的聯系;將工藝知識融入到后端的自動化設備(數控機床、焊接 機器人、自動切割機)應用中,實現三維工藝從產品設計--工藝--智能制造的貫穿式應用,全面提升行業加工智能性和效率。
5.建立了全制造過程可視化集成控制中心:將計劃、執行、物流、質量等業務板塊的實時決策數據與圖表集中展示,打通各功能域的關聯關系,建設可視化集成控制中心,打造實施過程數據驅動的制造車間決策支持平臺,支持 計劃、物流、質量、采供等多功能組織的全局協同生產與調度。
6.構建了基于企業私有云的分布式協同制造服務體系:通過建立面向3C制造的企業級私有云制造服務平臺,將勁勝精密分布在不同地域的7個事業部35個車間通過企業私有云進行連接,打造支持企業內多工廠協同制造的云服務模式,提升企業異地協同制造能力。
六、該創新為企業所帶來的效益
1.節省金屬加工環節的人力70%以上(以每日兩班生產基準,按照每人管理2.5臺機器,每機器人1拖2計算);
2.實現高速高精鉆攻中心、國產數控系統、機器人與收取料系統的協同運動控制,實現多種車間智能裝備之間的協同工作。
3.采用基于工藝知識庫的三維智能工藝規劃,提高研制效率;通過高級計劃排程和實時生產響應技術,減少設備空轉時間。
4.建立生產過程數據庫,充分采集制造進度、現場操作、設備狀態等生產現場信息;提高車間加工過程質量檢測自動化程度,建立產品質量追溯系統,實現全制造過程品檢數字化。
5.建立面向大批量快速響應生產的制造執行系統(MES),實現基于實時制造數據的可鉆取仿真車間。
6.可為企業每年新增8500萬元的營業收入,每年可為地方政府新增稅收300萬元。